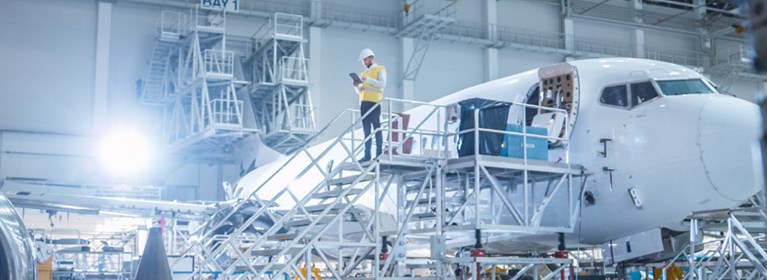
Manufacturing in Hazardous Environments
Manufacturing | Safety and Training | By Duff-Norton | Jul 18, 2019
Whether it’s a production environment involving automatic guided vehicles (AGVs) or a grain storage and processing facility, manufacturing environments are invariably prone to hazards and the potential for injury that comes with them.
The foundation for remaining vigilant and avoiding worst-case scenarios is understanding as much as possible about manufacturing hazards and how to avoid them. Thankfully, organizations like the Occupational Safety and Health Administration (OSHA) have done a lot of the research and learning on behalf of others, so it’s mostly a matter of taking the advice that’s available and then applying it to your manufacturing situation.
Here is a breakdown of the essential knowledge for manufacturing in hazardous conditions.
How are ‘hazardous conditions’ defined?
Hazardous conditions are fairly self-explanatory: they exist when materials are present that pose the risk of injury or major facility damage. The term is often used to refer to the risk of explosions or fires in manufacturing plants, but it can also be used to reference risks associated with human-machine interface (HMI) the use of machines, heavy weights, vehicles and more.
In short, if there are materials or conditions present that could harm someone if not properly handled, the situation is considered hazardous.
The classes and divisions of hazardous materials
Different materials require different precautions to avoid disaster, and as such, a system of classification is followed to help machine operators standardize their safety specifications.
Explosions and fires are at the front of many manufacturer’s minds, so these classifications pertain specifically to materials that are potentially combustible.
Hazardous materials are split into three classes, which define their type:
- Class I: Potentially explosive or flammable gases and vapors.
- Class II: Potentially flammable or conductive amounts of dusts.
- Class III: Potentially flammable amounts of fibers or flyings.
The risk level of the material’s presence is then defined by division to further drill down on the required safety specifications:
- Division I: Hazardous material is present in a potentially explosive or flammable amount under normal operating conditions.
- Division II: Hazardous material is only present in a potentially explosive or flammable amount in the event of a fault or other unexpected error.
Beyond class and division are group classifications, which go into more detail about the type of material and the safety requirements that surround it.
There is a full list in our post on explosion avoidance, found here.
The basics of explosion prevention
Because they represent one of the most serious hazards for manufacturers, explosions merit special attention. There are several basic steps that can be taken to prevent them.
1. Perform a risk assessment
This applies to all hazards in the working environment. A thorough risk assessment that takes all dangerous materials and machinery into account should be performed as regularly as is feasible to give managers a full idea of the safety challenges their factory presents.
2. Ensure equipment is of the correct specification
All machinery that involves the three elements of a potential explosion (fuel, oxygen and heat) must be of the correct safety specification for the environment it’s being used in. There are different methods for enclosing hazardous materials. This should reference the class and division of the materials being used, and safe operating temperatures should be clearly marked.
An exhaustive list of enclosure methods can be found here.
3. Maintain equipment regularly
A regular maintenance schedule should be in place to guarantee that equipment is in working order. Special attention should be paid to enclosures, which should be checked for potential leaks and cleared of any layers of dust or debris that may cause an unwanted increase in temperature.
Any maintenance, whether for explosion prevention or otherwise, should be performed using OSHA’s ‘Lock-Out Tag-Out’ procedure, found here.
4. Train staff to deal with hazardous materials
All staff coming into contact with hazardous conditions or materials should be fully trained in machine operation and safety procedures, with regular refresher training to prevent complacency or over-confidence that could lead to human error.
Other common hazards for manufacturers
Explosive materials are not the only source of risk when manufacturing in hazardous conditions. There are several more common dangers that contribute to a hazardous work environment. The following are some of the most common, but it is important to perform a risk assessment to identify the unique risks of individual manufacturing plants, including:
1. Falls
In 2017 alone, 366 construction workers lost their lives to preventable falls. In 2018, the Bureau for Labor Statistics (BLS) recorded 240,160 slips, trips or falls that resulted in injury. Fall hazards should be identified in any manufacturing space, and staff should be trained to spot risks and remain vigilant.
OSHA’s Fall Prevention Campaign has produced useful, free resources to educate employers and staff alike.
2. Electrical exposure
There were more than a thousand injuries caused by ‘exposure to electricity’ found by the BLS. Equipment and factory maintenance can prevent electrical faults and shocks, as well as electricity-specific safety training for workers.
3. Injuries caused by machinery
The BLS recorded tens of thousands of incidents involving workers being seriously injured by machinery in 2018. These included everything from people getting caught in machinery to having broken components fall on them from a height.
The aforementioned diligence in operation and safety training is the best preventative measure that manufacturers can take in this instance, as is regular maintenance and the provision of safety guards or barriers. The same precautions should be taken for any manufacturer that makes use of automated guided vehicles.
Fail-safe machinery
A significant majority of the hazardous conditions mentioned above involve the interaction between human workers and their machine counterparts. For this reason, it’s crucial to plan ahead and invest in machinery with the appropriate safety measures and fail-safes.
Maintenance has featured heavily, as well. A key factor in the maintenance equation is the ability to take preventative action before machinery has the chance to fail. Wear-indicator nuts of the kind we produce do just this, and they combat the danger of human injury in the process.
Duff-Norton wear-indicator nuts are designed to flag the state of repair of screw jacks that, in many cases, bear significant loads. In installing wear-indicator nuts, it is possible to plan vital repairs that will prevent injury and factory down-time.
Actuators, too, present a source of potential risk. Our actuators – which are more precise, predictable and programmable than their hydraulic counterparts – are fitted with fail-safe ball screws, designed to bear weight in the event of a power outage or malfunction.
Choosing ball screw actuators with wear indicator nuts aren’t the only preventative measures worth taking, but they represent the serious nature with which safety should be approached in a manufacturing environment.
Potentially Hazardous conditions of any kind should be treated with a proactive, not reactive, response.
Contact Our Engineering Team For A Free Application Analysis
Lift, Position, and Support with Columbus McKinnon Screw Jacks
Learn everything you need to know about the screw jacks available from Columbus McKinnon including the two types of screw jack systems, the main types of screw jacks (machine and ball) and, available features (stainless steel, anti-backlash, ,heavy-duty and more).
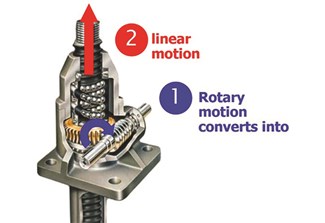