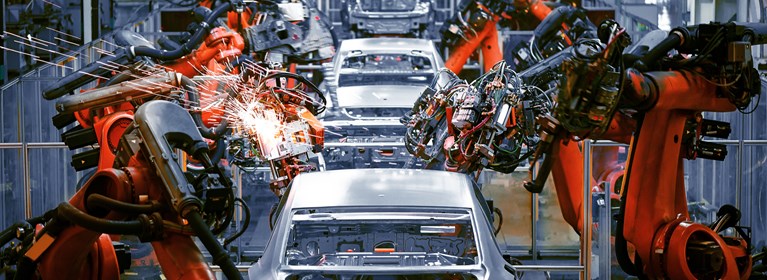
Upskilled by Robots: How Automation Will Empower Your Labor Force
Manufacturing | Industry News | By Duff-Norton | Jan 15, 2020
Technology is a tool to give human beings superpowers, right? Often, automation is seen as the next step: taking humans out of the equation entirely. History tells us that with advancing technology, the labor force needs to adapt and learn new skills, especially when it comes to roles that are repetitive and/or physically demanding.
The plow saves the farmer hours of back-breaking work. ‘Piecers’ no longer have to fix broken threads on textile spinning machines – a dangerous and exhausting job that was once done by small children.
With current technologies, automation is another wake-up call for the workplace to adapt, but it’s the start of something bigger. Between 39 million and 73 million jobs in the US could be lost to automation, says a report by the McKinsey Global Institute. Clearly, there are society-wide implications. However, there are also plenty of opportunities to sustainably empower your labor force over the long term, particularly in the manufacturing sector.
Reduce time spent in dangerous environments
Or, dull environments. Automation is perfect for repetitive manufacturing processes. For example, robotic arms with delicate grips can pack soft fruits into crates, ready for the store.
More importantly, humans can avoid being exposed to dangerous or toxic environments. According to the Bureau of Labor Statistics, there were 5190 fatal injuries at work in 2016, the first time more than 5000 fatalities have been recorded since 2008. The causes? Varied, but a major factor is exposure to harmful substances or environments, which rose by 22 percent on the previous year. Automation means less risk to human life. We like that.
Increase production and boost the economy
Take Siemens’ Amberg Electronics Plant in Germany. According to this article, they’ve increased productivity by more than one thousand percent over the past 25 years – but, the number of employees has remained the same. The local economy and standard of living for those employees and their families has improved as a result.
Diversify offerings
There is always room for the human element. Nowadays, the handmade, the artisanal, the crafted – these are seen as luxury sell-points. Celebrate the human touch and take advantage of automation. Then sell to different markets.
Shift focus to other stages
Now you can spend more time on quality control or customer service. These days, manufacturing isn’t just about making and selling a product. The expectations are higher, especially when it comes to customer communication. Your labor force knows the product, so use that knowledge to help the buyer and ensure your offering stands out as the best. The numbers add up: many of the fastest-growing occupations for 2016-2026 are service-related.
Invest in skills training
This is the big one. Automation means certain jobs will become obsolete. But it also means new jobs will be created, and they will need skilled people to take them on. We’ve talked before about how there’s a growing skills gap in manufacturing, with retiring workers leaving jobs that aren’t being filled. Training your workers to fill these and newly emerging roles is vital – and robots can’t do them.
Your workers want to learn, grow and progress. Take advantage of the human capacity for complex reasoning and communication and train them to meet requirements. It doesn’t have to mean everyone on the factory floor becomes an engineer. Soft skills matter too, and training in communication, leadership or project management can empower your employees to innovate. This will drive your business into the future.
The future is now
If you’re a manager, use this opportunity to make the most of your labor force. And if you’re worried that automation is going to put you out of a job, be prepared to grow. It can be uncomfortable, but it’s part of life.
Duff-Norton
As a leading engineering manufacturer of reliable industrial lifting and positioning products, Duff-Norton is comprised of individuals with in-depth industry experience. Articles authored by Duff-Norton belong to a collection of blogs written by product and application experts throughout the organization.
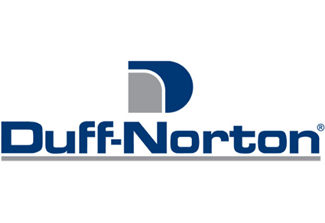