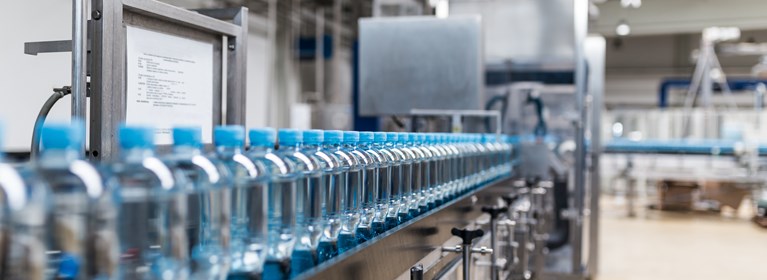
Automated Mill Roll Handling System
Food Processing & Beverage | Crane Systems | By Magnetek | Jul 11, 2006
Background
The demand for plastic food packaging has greatly increased over the last few years, resulting in new production lines to accommodate the increase in volume. One manufacturer required a new production line that would increase the overall production capacity by 25%, and would be compatible with their existing WIP/SLIM system in the facility (the plant scheduler responsible for notifying production of which product is required). Like most manufacturing facilities, space was at a premium and labor was expensive. Therefore, this system had to produce and store large amounts of film in a relatively small area, while requiring minimal people to oversee the operation.
System Description
The newly installed production line uses three main machines for producing film. The first machine is the Orienter. The Orienter takes plastic pellets and produces film on large 20-foot stainless steel cores. The second machine is the Slitter. The Slitter cuts the film to desired widths and lengths for sale to the food packagers. The third machine is the Slabber. The Slabber cuts unusable material off of the core and dispositions the material to scrap. Two fully automated cranes operating on parallel runways are responsible for moving the cores between the machines and the warehouse locations. The In-Line Crane services the Orienter, Slitter, and a small warehouse location called the In-Line WIP.
The Side Crane services the Slitter and a main warehouse location called the Side WIP. Both the In-Line and Side Cranes are similar in design and capacity. However, the Side Crane has a rotate motion that can change the core orientation when the Slitter requires material unreeled in the opposite direction. Two shuttle cars are used to transfer the cores between the two bays. Shuttle #1 can carry two cores. One of the core locations is reserved for only empty cores, while the other can carry an empty or full core. Shuttle #2 can carry only one core. This core can either be empty or rolled with film.
Each crane and shuttle has an on-board Allen-Bradley SLC 5/05 Ethernet PLC. These PLCs are responsible for manual and automatic motion of the cranes and shuttles. All hoist motors in the system are controlled by Electromotive IMPULSE®•VG+ Series 2 Vector Drives. All other motors are controlled by Electromotive IMPULSE®•G+ Series 2 Adjustable Frequency Drives. An additional SLC 5/05 PLC is located in a floor-mounted enclosure and is responsible for controlling various safety gates and walkways surrounding and within the production area.
Two desktop PCs are the backbone of this automated crane system. These PCs provide inventory, traffic, and communications control. The main server PC is located in the computer room. An additional PC, located in the control room, acts as the back-up server. Both PCs run SoftLogix5 control software and both can control the entire system. Under normal operation the main server is active and the back-up server is inactive. The active server is in charge of the system. The only function of the inactive server is to monitor the system. In the event of an active server failure, the inactive server is made active by the touch of a button. The back-up server is running RSView32 operator interface software, which allows operators to monitor the system. Two additional industrial strength touch-screen PCs are located on the plant floor. These PCs also run RSView32 operator interface software.
The active server is used to manage the Ethernet communications between the PLCs and PCs. This network allows vital information to flow between equipment. A big advantage of the Ethernet network is that it allows maintenance personnel to troubleshoot and monitor the PLC control programs from the floor. A hardwired communications link between the shuttle’s PLCs and the other equipment was not practical. To solve this issue, Ethernet RF modems are used for this communication means.
Even though one server is active and one is inactive, both servers keep track of inventory. Every core has an ID that the system uses to identify it. Each core has an RFID tag that identifies not only the core, but also the core orientation. When a crane is given a command to pick-up a core it’s not only given the location, but also the core ID. When the crane picks up the core it identifies the core using an RFID reader. This RFID application was particularly difficult to solve because the RFID tag had to be mounted inside the stainless steel core and the reader had to be positioned in such a fashion that it would not get damaged while retrieving and transporting the cores.
System Operation
Automatic Mode of Operation
Orienter
An empty core is automatically delivered to the Orienter. The Orienter produces film and rolls it on the core. When a core is ready to be removed from the Orienter, the Orienter sends a hard-wired signal to the crane system. The In-Line Crane removes the core and places it on an available shuttle. The shuttle moves the core to the QC area where the film is inspected. The film is then tagged and the core is released to the Side WIP for storage.
Slitter
When the Slitter requires film, a hardwired signal is sent to the crane system. The crane system then sends a message to the WIP/SLIM to define a new assignment. When the new assignment is received, the cranes and shuttles find and retrieve the core. The core is typically at the Side WIP, but it may be at the In-Line WIP. If the core orientation does not match the Slitter requirement, the core is sent to the Side Crane for rotation. After a core is delivered, the core that was previously slit is removed.
Slabber
When the Slabber requires a core to be slabbed, the operator requests the next core by pressing a button at the Slabber push-button station. After receiving the push-button input, the crane system sends a message to the WIP/SLIM to request the next assignment. When the new assignment is received, the cranes and shuttles deliver the core to the Slabber. After the Slabber has removed all the material from the core, the operator returns the core to the automated system by pressing a button at the Slabber push-button station. The cranes and shuttles move the core to an empty WIP location.
Manual Mode of Operation
An Electromotive SBP2 pendant is used for manual back-up operation while performing system maintenance.