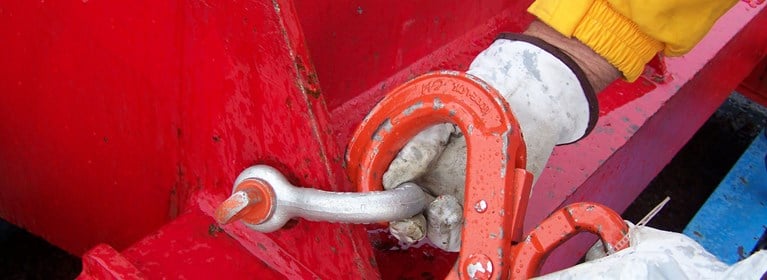
Understanding Safety and Design Requirements of Below-the-Hook Lifters
When it comes to below-the-hook lifters, there are standards in place, including ASME B30.20 and BTH-1, that outline the design, manufacture, use and inspection of this equipment.
Hoisting & Lifting | Rigging | Safety and Training | By Henry Brozyna | Oct 05, 2020
There are countless lifters in the field made to solve lifting issues and speed up the lifting process. Let's look at below-the-hook lifting devices and the safety and design requirements of below-the-hook lifters.
What is a below-the-hook lifting device?
The American Society of Mechanical Engineers (ASME) states that a below-the-hook lifting device, or below-the-hook lifter, is "a device used for attaching a load to a hoist. This device may contain components such as slings, hooks, and rigging hardware."
Below-the-hook lifters are tools or mechanical devices that secure a load that is connected to an overhead crane or hoist for safe transport from one location to another.
While many of these lifters are “homemade,” that in itself does not disqualify them from service. What typically disqualifies a lifter from service is the lack of labeling, ID tags or engineering to back up the design.
When it comes to below-the-hook lifters, there are standards in place, including ASME B30.20 and BTH-1, that outline the design, manufacture, use and inspection of this equipment.
Determining the Design Category
Let’s start with the design per ASME BTH-1.
Two of the most important things that help dictate the design of a lifter are the load that will be lifted and the environment the lifter will be used in.
The most common design classification is Design Category B that has a minimum 3:1 safety factor. “Design Category B should be designated when the magnitude and variation of loads applied to the lifter are not predictable or where the loading and environmental conditions are severe or not accurately defined.” This category would include most engineered spreader beams.
Identifying the Service Class
Once the design is established, BTH-1 specifies the lifter must be rated for a Service Class. The Service Class takes into account the number of load cycles a lifter will see during its lifespan.
Every time a lifter is used, it flexes, and if it flexes enough times it will fracture – this is called Fatigue. Fatigue needs to be taken into consideration to ensure safety and long life of the lifter.
Three questions that will help the engineer determine Fatigue and the Service Class of the lifter are:
- How long do you plan on using this lifter?
- How many times a day will the lifter be used?
- What capacity loads do you expect to be lifting?
In BTH-1, the most common Service Class is 2, which rates the lifter for 100,001 - 500,000 load cycles.
Selecting Materials and a Design
Once the Design Category and Service Class are established, the engineer can select the material and determine a design for the lifter that meets both the specifications and a 3:1 design factor. The material must be of sufficient strength to handle the design forces and safety requirements, but also economical for the customer’s needs.
One important element of lifter design is the welds. All welds on a lifter need to be done per ANSI/AWS D14.1.
Tagging the Lifter
Once the lifter is designed and built, it must be tagged. If a lifter weighs more than 100 lbs., the weight of the lifter must appear on the tag. The tag is a very important part of any lifter. It shows who built it, what its working load limit (WLL) is and the design criteria used.
In some cases, lifters will employ motors. If so, electrical information must also appear in the tag, including amps and voltage requirements. The tag is usually placed in an area where it is least likely to be damaged, such as near the hook attachment or bail. Also on some C-Hook or coil lifters, the tag can be placed behind the counterweight. The location is selected to minimize damage to the tags.
Using Lifters Safely & Correctly
Now that you have a lifter built to all applicable standards and specifications, what is your responsibility as an owner? The person using the lifter must be trained properly. They must be familiar with the safe and proper way to use a lifter. They must also know how to visibly inspect the lifter at the start of each shift – this is called a frequent inspection. Frequent inspections are not mandatory, but they are an important step to take before using a lifter.
Also, per ASME B30.20 there is an “every lift inspection” B30.20-1.3.2, requirement. The operator shall inspect before and during every lift for damage. The surface of the load shall be free of any debris. If the lifter is powered the operating controls should be in good working order & any indicators that are installed to monitor the power aspects of the lifter should be in good working order.
A more thorough inspection of at least once a year must also be done – this is a periodic inspection. The frequency of the periodic inspection is determined, in part, by the severity of use of the lifter. Simply put, the more you use something the more it will need to be inspected. We also need to consider the environment the lifter is used in. Depending on the severity of use and the environment, a periodic inspection could be required as often as quarterly. Records of periodic inspections must be kept. For all of the requirements of a periodic inspection, see ASME B30.20-1.3.4.
Next time you see a lifter being used that does not have tags or calculations to back up its design, you can safely assume it is unsafe to use. Your lifters must be made by a reputable manufacturer. Or, if you choose to make them yourself, remember to follow all of the standards that are put in place to keep you and/or your associates safe.
At Columbus McKinnon offers an extensive portfolio of below-the-hook lifting devices to ensure safe, efficient lifting, ranging from low headroom and high capacity to load leveling and multiple-point lifts. Stay on top of lifting and rigging best practices with online and in-person training offerings with Columbus McKinnon's team of expert trainers
Henry Brozyna
Henry Brozyna is an Industry Product Trainer at Columbus McKinnon specializing in Crane and Hoist Inspection and Repair, Rigging & Load Securement He has been training on crane and rigging safety for more than 20 years. Henry is a member of the Tie Down committee and former Board of Directors for the WSTDA; this group writes the standards that are used by the material handling industry, the transportation industry, and also law enforcement. Henry is also a current member of the Crane Institute’s board of directors.
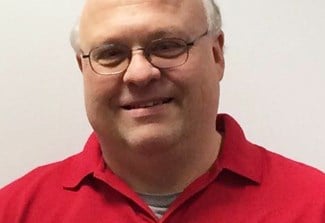