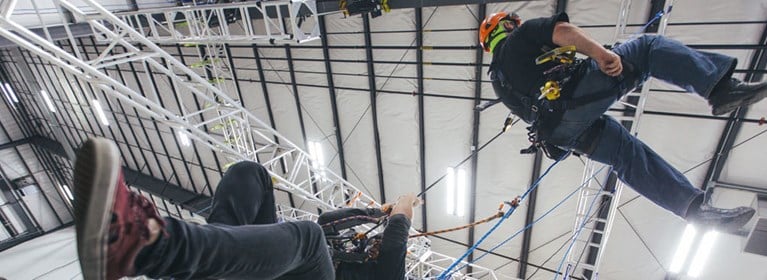
Charpy Evaluation of Rigging Hardware
Rigging | By Troy Raines | Sep 16, 2019
For those of you who work in the material handling industry, you may have heard of Charpy values. If you have heard this term, do you know what it means?
A Charpy value is the measurement of the toughness of a material and is determined by performing a Charpy impact test. The Charpy impact test utilizes a swinging weight to strike a sample of material that has been machined to specific tolerances and notched. In many instances, the sample is also cooled to very low temperatures to simulate colder climates and seasons of the year. The distance the weight swings past the sample indicates how much force (measured in joules, ft-lbs.) it took to break the sample. That force is the Charpy value (named after Georges Charpy who came up with this methodology).
So, why am I talking about Charpy values?
Many manufacturers offer high Charpy value shackles and master links for use in extreme conditions. This always struck me as odd and brings up three questions in my mind:
- Why offer high Charpy values in shackles and master links and very few other rigging products?
- Is a Charpy value even relevant in general lifting?
- What is the Charpy value of leading manufacturers?
Finding answers to these questions was not an easy task and proved to be an expensive undertaking, so I want to share what I found with you to save you both time and money.
1. Why offer Charpy values in shackles and master links and very few other rigging products?
I haven’t found a logical answer to this one yet. For example, in the offshore industry, I was told that most rigging is done with wire rope slings and, normally, these slings do not have hardware attached. And, another oddity is that master link standards only require a Charpy value test on the weld.
Then, there are other types of slings and hardware that do not have Charpy requirements being used in the same conditions, but these aren’t failing. So, this begs the question, why is a Charpy requirement needed on shackles and master links? Is it only done because they are easier to manufacture with a high Charpy? These products usually have a lower hardness than hooks and mechanical coupling links and, as a general rule, Charpy values are lower the higher the hardness. If you have additional insight, I’d really appreciate you sharing in the comments section at the end of this blog.
2. Is a Charpy value even relevant?
At first I thought maybe. There is a possibility that rigging products wouldn’t significantly deform before failure at lower operating temperatures. But, from what I have found so far, modern steels commonly used in rigging equipment stay ductile in really low temperatures. Therefore, I think there’s a need for additional testing of rigging product ductility at -20°C to determine if having a Charpy requirement improves performance at these temperatures. Have any of you done a test like this before? If so, please let me know in the comments section below.
Another theory justifying high Charpy requirements for rigging equipment is that cracks will spread slower in materials with a high Charpy value. But, I also learned that a product with a low Charpy value is no more likely to fail unless it already has a crack. With that said, it seems that a higher Charpy value might be desirable in an extreme environment, especially where inspection is more difficult and failure more likely. But, we all know cracked hardware shouldn’t be used. Every standard says cracks are a “removal from service” criteria, so this doesn’t make sense.
Proving the Relevance of the Charpy Value with Real World Experiences
To prove or disprove the relevance of the Charpy value, I interviewed hundreds of industry experts with more than a thousand years of cumulative experience. In all of these interviews, I only heard of two stories related to equipment failures that might involve Charpy values.
The first story is that a shackle failed due to impact at “normal” temperatures while other hardware was being tested. Further investigation revealed a reputable high Charpy value manufacturer made the shackle and it was being used with a wrecking ball. This proves that even high Charpy value products can be abused to failure.
The second story was a reported failure of chains breaking during winter construction of a Canadian diamond mine at -60°F. The issue here was that these were traction chains wrapped around the tires of an earthmover. No one I interviewed was aware of a failure related to low-temperature toughness in lifting components.
So why were there no known failures of rigging equipment with no Charpy requirements? Was it because people know better than to use worn or damaged products? Was it because a Charpy test only evaluates the material without considering the product design? Regardless, these interviews did not give me a justifiable reason to add cost to a product for general lifting applications.
3. What is the Charpy value of leading manufacturers?
My third question was the most expensive part of my research. To answer this, I acquired samples of different rigging products from different regions and manufacturers and put them through a Charpy test. In total, I tested 44 products from 8 countries.
I only tested common types of hardware from well-known reputable manufacturers. Tests were conducted at an independent third party lab to EN 10045. Load pins were not tested as they are generally a higher hardness with lower toughness. Samples are also generally too small for standard samples.
Charpy Value Testing Details
- Master links: We tested 18 products from 6 brands made in 5 countries. Most were “DNV Type Approved,” which requires high Charpy values. Results ranged from 8 to 158 Joules.
- Hooks: We tested 6 products from 4 brands made in 4 countries. Results ranged from 10 to 34 Joules.
- Shackles: We tested 16 products from 3 brands made in 2 countries. Results ranged from 16 to 113 Joules.
- Mechanical coupling links: We tested 4 samples from 4 brands made in 4 countries. Results ranged from 7 to 70 Joules.
Testing Results
Testing revealed a high degree of variation, even within a product type or manufacturer. The lowest value was 7 Joules and the highest was 158 Joules.
Conclusion
If lack of toughness as demonstrated by high Charpy values was an issue, this type of variation among large, reputable, international companies would cause related failures to be common occurrences. Since these types of failures are not common, adding a toughness requirement is an undue and disruptive burden on the market. Based on these findings, any general lifting product standard should not require a Charpy value. Doing so would favor a minor portion of rigging hardware manufacturers and increase cost without justification.
Troy Raines
Troy Raines is Columbus McKinnon’s Chain and Rigging Product and Engineering Manager. He joined the company in 2005 as a general engineer, supporting quoting specials, product design, and manufacturing engineering initiatives.
Today, Troy plays a key role in the development and support of rigging products and contributes to several major industry standards. He is a member of the ASME B30.9 (Slings), B30.20 (Below-the-Hook Lifting Devices), and BTH-1 (Design of Below-the-Hook Lifters) committees. He also serves as an alternate on B30.10 (Hooks) and B30.26 (Rigging Hardware), and is active on multiple Web Sling and Tiedown Association technical committees, as well as ISO/TC 111/SC1 and SC3.
Outside of work, Troy is proud of his military service and his role as a father to three sons.
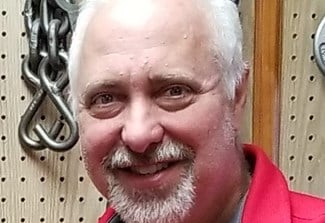