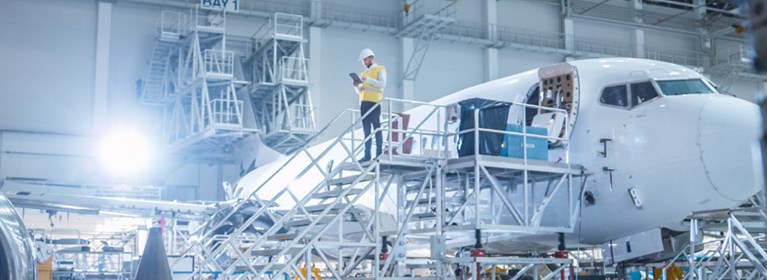
Fabricación en entornos peligrosos
Manufacturing | Seguridad y formación | Por Duff-Norton | 18 jul. 2019
Ya sea que se trate de un entorno de producción que involucre vehículos guiados automáticos (AGV) o una instalación de almacenamiento y procesamiento de granos, los entornos de fabricación son invariablemente propensos a los peligros y al potencial de lesiones que conllevan.
La base para permanecer alerta y evitar los peores escenarios es comprender tanto como sea posible sobre los peligros de fabricación y cómo evitarlos. Afortunadamente, organizaciones como la Administración de Seguridad y Salud Ocupacional (OSHA) han investigado y aprendido mucho en nombre de otros, por lo que es principalmente una cuestión de tomar el consejo que está disponible y luego aplicarlo a su situación de fabricación.
Aquí hay un desglose de los conocimientos esenciales para la fabricación en condiciones peligrosas.
¿Cómo se definen las "condiciones peligrosas"?
Las condiciones peligrosas se explican por sí mismas: existen cuando hay materiales presentes que representan el riesgo de lesiones o daños importantes en las instalaciones. El término se usa a menudo para referirse al riesgo de explosiones o incendios en las plantas de fabricación, pero también se puede usar para hacer referencia a los riesgos asociados con la interfaz hombre-máquina (HMI), el uso de máquinas, pesos pesados, vehículos y más.
En resumen, si hay materiales o condiciones presentes que podrían dañar a alguien si no se manejan adecuadamente, la situación se considera peligrosa.
Las clases y divisiones de materiales peligrosos
Los diferentes materiales requieren diferentes precauciones para evitar desastres, y como tal, se sigue un sistema de clasificación para ayudar a los operadores de máquinas a estandarizar sus especificaciones de seguridad.
Las explosiones y los incendios están en la mente de muchos fabricantes, por lo que estas clasificaciones se refieren específicamente a los materiales que son potencialmente combustibles.
Los materiales peligrosos se dividen en tres clases, que definen su tipo:
- Clase I: Gases y vapores potencialmente explosivos o inflamables.
- Clase II: Cantidades de polvo potencialmente inflamables o conductoras.
- Clase III: Cantidades potencialmente inflamables de fibras o voladores.
El nivel de riesgo de la presencia del material se define por división para profundizar en las especificaciones de seguridad requeridas:
- División I: El material peligroso está presente en una cantidad potencialmente explosiva o inflamable en condiciones normales de funcionamiento.
- División II: El material peligroso solo está presente en una cantidad potencialmente explosiva o inflamable en caso de falla u otro error inesperado.
Más allá de la clase y la división están las clasificaciones grupales, que entran en más detalle sobre el tipo de material y los requisitos de seguridad que lo rodean.
Hay una lista completa en nuestra publicación sobre cómo evitar explosiones, que se encuentra aquí.
Los fundamentos de la prevención de explosiones
Debido a que representan uno de los peligros más graves para los fabricantes, las explosiones merecen una atención especial. Hay varios pasos básicos que se pueden tomar para prevenirlos.
1. Realizar una evaluación de riesgos
Esto se aplica a todos los peligros en el entorno de trabajo. Una evaluación exhaustiva de riesgos que tenga en cuenta todos los materiales y maquinarias peligrosos debe realizarse con la mayor regularidad posible para dar a los gerentes una idea completa de los desafíos de seguridad que presenta su fábrica.
2. Asegúrese de que el equipo sea de la especificación correcta
Toda la maquinaria que involucre los tres elementos de una explosión potencial (combustible, oxígeno y calor) debe tener la especificación de seguridad correcta para el entorno en el que se está utilizando. Existen diferentes métodos para encerrar materiales peligrosos. Esto debe hacer referencia a la clase y división de los materiales que se utilizan, y las temperaturas de funcionamiento seguras deben estar claramente marcadas.
Una lista exhaustiva de los métodos de cerramiento se puede encontrar aquí.
3. Mantenga el equipo regularmente
Se debe establecer un programa de mantenimiento regular para garantizar que el equipo esté en buen estado. Se debe prestar especial atención a los recintos, que deben verificarse en busca de posibles fugas y limpiarse de cualquier capa de polvo o escombros que pueda causar un aumento no deseado de la temperatura.
Cualquier mantenimiento, ya sea para la prevención de explosiones o de otro tipo, debe realizarse utilizando el procedimiento 'Lock-Out Tag-Out' de OSHA, que se encuentra aquí.
4. Capacitar al personal para que se ocupe de materiales peligrosos
Todo el personal que entre en contacto con condiciones o materiales peligrosos debe estar completamente capacitado en el funcionamiento de la máquina y los procedimientos de seguridad, con capacitación de actualización regular para evitar la complacencia o el exceso de confianza que podría conducir a errores humanos.
Otros peligros comunes para los fabricantes
Los materiales explosivos no son la única fuente de riesgo cuando se fabrican en condiciones peligrosas. Hay varios peligros más comunes que contribuyen a un entorno de trabajo peligroso. Los siguientes son algunos de los más comunes, pero es importante realizar una evaluación de riesgos para identificar los riesgos únicos de las plantas de fabricación individuales, que incluyen:
1. Caídas
Solo en 2017, 366 trabajadores de la construcción perdieron la vida por caídas prevenibles. En 2018, la Oficina de Estadísticas Laborales (BLS) registró 240,160 resbalones, tropiezos o caídas que resultaron en lesiones. Los peligros de caída deben identificarse en cualquier espacio de fabricación, y el personal debe estar capacitado para detectar riesgos y permanecer vigilante.
La Campaña de Prevención de Caídas de OSHA ha producido recursos útiles y gratuitos para educar a los empleadores y al personal por igual.
2. Exposición eléctrica
Hubo más de mil lesiones causadas por la "exposición a la electricidad" encontrada por el BLS. El equipo y el mantenimiento de la fábrica pueden prevenir fallas eléctricas y descargas, así como la capacitación de seguridad específica de electricidad para los trabajadores.
3. Lesiones causadas por maquinaria
El BLS registró decenas de miles de incidentes que involucraron a trabajadores gravemente heridos por maquinaria en 2018. Estos incluían todo, desde personas atrapadas en la maquinaria hasta que los componentes rotos caían sobre ellos desde una altura.
La mencionada diligencia en la operación y la capacitación en seguridad es la mejor medida preventiva que los fabricantes pueden tomar en este caso, al igual que el mantenimiento regular y la provisión de protectores o barreras de seguridad. Se deben tomar las mismas precauciones para cualquier fabricante que haga uso de vehículos de guiado automatizado.
Maquinaria a prueba de fallos
Una mayoría significativa de las condiciones peligrosas mencionadas anteriormente involucran la interacción entre los trabajadores humanos y sus contrapartes de la máquina. Por esta razón, es crucial planificar con anticipación e invertir en maquinaria con las medidas de seguridad adecuadas y a prueba de fallas.
El mantenimiento también ha tenido un gran protagonismo. Un factor clave en la ecuación de mantenimiento es la capacidad de tomar medidas preventivas antes de que la maquinaria tenga la oportunidad de fallar. Las tuercas indicadoras de desgaste del tipo que producimos hacen precisamente esto, y combaten el peligro de lesiones humanas en el proceso.
Las tuercas indicadoras de desgaste Duff-Norton están diseñadas para marcar el estado de reparación de los gatos de tornillo que, en muchos casos, soportan cargas significativas. Al instalar tuercas indicadoras de desgaste, es posible planificar reparaciones vitales que evitarán lesiones y tiempo de inactividad de fábrica.
Los actuadores también presentan una fuente de riesgo potencial. Nuestros actuadores, que son más precisos, predecibles y programables que sus homólogos hidráulicos, están equipados con tornillos de bolas a prueba de fallos, diseñados para soportar peso en caso de un corte de energía o mal funcionamiento.
La elección de actuadores de tornillo de bolas con tuercas indicadoras de desgaste no son las únicas medidas preventivas que vale la pena tomar, pero representan la naturaleza seria con la que se debe abordar la seguridad en un entorno de fabricación.
Las condiciones potencialmente peligrosas de cualquier tipo deben tratarse con una respuesta proactiva, no reactiva.